PART 2: Checking The Fuel Injector Spray Pattern
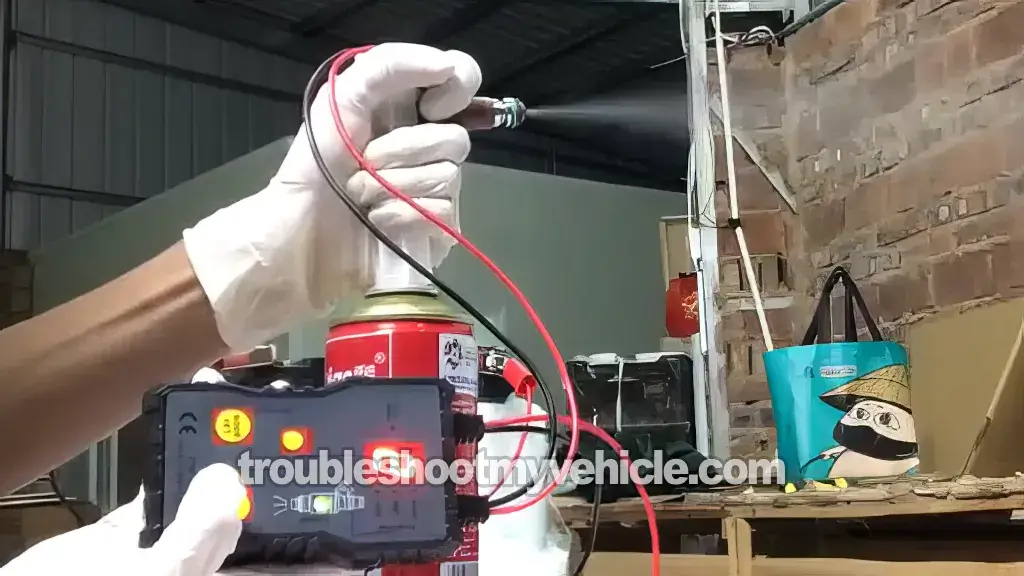
Up to now, you've confirmed that the internal resistance of the fuel injector is within the specified range, indicating it doesn't have an open or short-circuit problem.
The next step is to remove the fuel injector and, using a DIY fuel injector cleaning tool you can purchase online along with a spray can of brake cleaner, activate it to see if it actually sprays.
This fuel injector cleaning tool kit comes with two important components:
- A 12 Volt power module that'll allow you to trigger the fuel injector in pulses -just like the fuel injection computer does.
- An adapter that'll allow you to connect the fuel injector to a spray can of brake cleaner.
Once you've set up the test, if the fuel injector isn't clogged, it'll spray the brake cleaner in a fine mist. If the injector is clogged or malfunctioning, it'll just squirt the brake cleaner out or not at all.
The cool thing about this fuel injector cleaner took kit is that it's not expensive. You can purchase it here:
- QX Fuel Injector Tester & Adapter for Diagnosis and Cleaning of Injectors DIY Cleaning Tool Kit (at: amazon.com).
- EM276SET Fuel Injector Tester & Adapter DIY Cleaning Tool Kit Set (at: amazon.com).
IMPORTANT: Before installing the same or new fuel injector back on the fuel injector rail, take a look at: Important Tips For Installing A Fuel Injector.
CAUTION: Use safety glasses when performing the fuel injector cleaning procedure.
Alright, these are the test steps:
- 1
Remove the fuel injector.
- 2
Connect the fuel injector to the plastic adapter.
NOTE: I've found that securing the fuel injector to the adapter with a thick rubber band helps to make the whole process easier and less messier. - 3
Connect the fuel injector to the tool's power module.
NOTE: Follow the tool's safety and recommended set-up instructions. - 4
Connect the cleaning kit's power module to your van's battery.
- 5
Connect the fuel injector/adapter to a spray can of brake cleaner and press them onto the spray can.
- 6
Activate the power module.
- 7
The fuel injector should spray fuel in a fine mist and in a conical shape.
Let's interpret your test result:
CASE 1: The fuel injector did not spray at all. This tells you that the fuel injector is bad and needs to be replaced.
CASE 2: The fuel injector sprayed the brake cleaner in a fine mist and in a conical pattern. This tells you that the fuel injector is OK.
CASE 3: The fuel injector sprayed the brake cleaner in a squirt or a stream (not in a fine mist). This tells you that the fuel injector is dirty/clogged.
Continue cleaning the fuel injector until it starts to spray in a fine mist. If the cleaning it doesn't restore the injector's spray pattern to that of a fine mist, you'll need to replace it.
Important Tips For Installing A Fuel Injector
When installing a fuel injector (whether it's the same one or a new one) on the fuel injector rail, keep in mind the following important suggestions to ensure everything runs smoothly and safely.
- Always use new fuel injector O-rings: If you're reinstalling the same fuel injector (a new fuel injector will come with new O-rings), it should never be installed with its old O-rings. This is crucial for creating a tight seal and preventing fuel and vacuum leaks.
- Lubricate the new fuel injector O-rings: Before installing the new O-rings on the fuel injector, make sure to lubricate both with a bit of clean (new) engine oil (don't use any silicone based grease or lubricant).
Lubricating the O-rings makes it easier to slide the fuel injector into the injector rail and into the intake manifold injector port without damaging them. A damaged O-ring can cause fuel or intake manifold leaks, which is exactly what you want to avoid. - Replace damaged connector: If the fuel injector's connector is damaged in any way, replace it with a new one. It's not uncommon for the locking tab of the fuel injector to break; if it's broken, replace the connector.
Also, avoid using butt connectors to join the new connector's wires to the engine wiring harness. Instead, solder the wires for a permanent repair, as butt connectors are infamous for becoming loose and causing false contact issues.
Remember, the whole idea here is to prevent gasoline leakage and avoid the risk of a fire. So take your time and ensure everything is properly seated and secure.
More 4.6L Ford E150, E250, And E350 Test Tutorials
If this tutorial was helpful, be sure and take a look at all of the 4.6L V8 E150, E250 and E350 diagnostic tutorials and wiring diagrams in this index:
Here's a sample of the tutorials you'll find there:
- How To Test The Ignition Coils (2000-2009 4.6L, 5.4L V8 Ford E150, E250, E350).
- How To Test The CKP Sensor With A Multimeter (1997-2009 4.6L, 5.4L V8 Ford E150, E250, E350).
- How To Test For A Blown Head Gasket (1997-2003 4.6L, 5.4L V8 Ford E150, E250, E350).
- How To Test Engine Compression (1997-2007 4.6L, 5.4L V8 Ford E150, E250, E350).
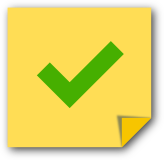
If this info saved the day, buy me a beer!
