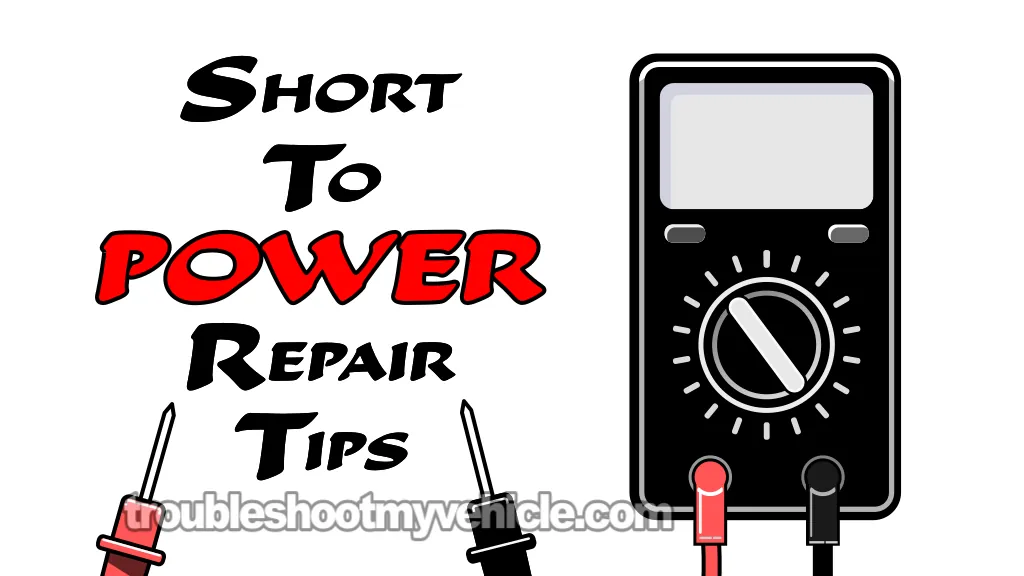
Finding 12 Volts on a sensor wire is never normal —and it's a clear sign that something's seriously wrong in the wiring harness.
If you're chasing a no-signal or sensor-related trouble code, and your multimeter suddenly reads battery voltage on a 5 Volt reference or sensor Ground wire, don't panic.
This guide will walk you through the most common real-world causes —things like melted wiring, fuse box damage, or rodent-chewed harnesses— and show you exactly where to look.
Contents of this tutorial:
APPLIES TO: This tutorial applies to the following vehicles:
- 1989-1993:
- Dodge Ram 150 Pickup 5.2L V8: 1989, 1990, 1991, 1992, 1993.
- Dodge Ram 250 Pickup 5.2L V8: 1989, 1990, 1991, 1992, 1993.
- Dodge Ram 150 Pickup 5.9L V8: 1989, 1990, 1991, 1992, 1993.
- Dodge Ram 250 Pickup 5.9L V8: 1989, 1990, 1991, 1992, 1993.
- Dodge Ram 350 Pickup 5.9L V8: 1989, 1990, 1991, 1992, 1993.
- 1994-2003:
- Dodge Ram 1500 Pickup 5.2L V8: 1994, 1995, 1996, 1997, 1998, 1999, 2000, 2001.
- Dodge Ram 2500 Pickup 5.2L V8: 1994, 1995, 1996, 1997, 1998.
- Dodge Ram 1500 Pickup 5.9L V8: 1994, 1995, 1996, 1997, 1998, 1999, 2000, 2001, 2002, 2003.
- Dodge Ram 2500 Pickup 5.9L V8: 1994, 1995, 1996, 1997, 1998, 1999, 2000, 2001, 2002.
- Dodge Ram 3500 Pickup 5.9L V8: 1994, 1995, 1996, 1997, 1998, 1999, 2000, 2001, 2002, 2003.
Short Circuits Vs. Open Circuits (And What A Short To Power Really Means)
Terms like "short-circuit", "open-circuit", or "short to power" can get confusing fast. So I'll break it down:
What's an Open-Circuit Problem?
- An open-circuit means that a wire is broken somewhere —or a connection is missing. Electricity can't flow because the path is incomplete.
- For example: a sensor wire that's been cut, corroded, or disconnected will show no voltage, no Ground, and no signal. The PCM can't read anything because the circuit is "open".
What's a Short-Circuit Problem?
- A short-circuit happens when electricity flows somewhere it's not supposed to.
- That usually means the wire's insulation is damaged and the copper inside is touching:
- Another wire.
- The engine block or chassis (Ground).
- Or a power source (like a 12V feed).
This kind of failure can cause sensors to read incorrectly, fry a PCM driver, blow a fuse, or even melt part of the harness.
Short to Ground vs. Short to Power
A short to Ground means a signal or power wire is touching the chassis or engine block —so electricity "escapes" before reaching its intended destination. It often leads to blown fuses or sensors that stop responding.
A short to Power (what this article is focused on) is when a wire that should only carry a small amount of voltage —like a 5 Volt reference or sensor Ground— gets connected to a 12 Volt power wire instead. This can confuse the PCM, damage internal circuits, and cause all sorts of sensor-related trouble codes.
Why this matters: This article focuses on diagnosing and fixing short to power problems —especially when you're seeing 12 Volts on a sensor wire that should only have 5 Volts or none at all.
That said, the methods and inspection tips here can also help uncover short to Ground issues, since many of the same wiring failures are involved.
So, in summary, keep in mind that open circuits stop signals. Shorts send signals the wrong way. Knowing the difference is what makes diagnosis accurate —and your repairs stick.
Common Causes Of A Sensor Circuit Short To 12 Volts
If you're seeing battery voltage (12 Volts or more) on a sensor wire that should only carry a 5 Volt reference, Ground, or signal voltage, it usually means that one of those wires has shorted to a nearby 12 Volt power feed wire.
Here are the most common causes I've seen in the shop:
1. Wiring harness damage from exhaust heat:
This is one of the most common causes. A section of the engine harness may have sagged or been routed too close to the exhaust manifold, header, or downpipe.
The extreme heat melts the protective loom and insulation, allowing wires to melt together —shorting a 5 Volt reference, Ground, or sensor signal wire to a nearby 12V power wire.
Oxygen sensor wiring is especially vulnerable here, and the sensing side of most O2 sensors gets Ground from the PCM —just like many other sensors.
If one of those wires melts into a 12V heater circuit wire, it can backfeed voltage into the PCM's sensor circuits and trigger a whole range of strange symptoms or trouble codes.
2. Chafed or pinched harness on a sharp engine edge:
Over time, heat, vibration, and engine movement can cause the harness to rub against brackets, the firewall, or the engine block.
Eventually, the plastic loom gets worn through —followed by the insulation on the wires inside. A sharp edge can slice right into the wire and short a 5 Volt reference, Ground, or signal wire directly to a 12 Volt feed.
3. Internal fuse box damage or melted terminals:
In some cases, the short originates inside the fuse box itself —whether under the hood or under the dash.
Check all fuse box slots for signs of heat damage, melted plastic, or deformed terminals.
If a connector has overheated or shorted inside the fuse block, it may have sent 12V down a circuit that was never supposed to carry it.
If you find signs of melting, you'll likely need to replace not just the fuse box, but also the section of the harness it connects to.
4. Rodent damage (chewed wires from rats or mice nesting in the engine bay)
Rats, mice, and even squirrels love engine bays. The warmth, shelter, and soft insulation on the wiring make it a perfect nesting spot.
One of the most common electrical issues I've seen on trucks that sit for extended periods —especially during colder months— is chewed wiring inside the engine harness.
Rodents often chew through multiple wires at once, sometimes stripping off only part of the insulation, and other times severing the wire entirely or shorting several wires together.
Look closely at the top of the intake manifold, behind the throttle body, around the battery tray, and near the firewall or brake booster.
You'll often see shredded wire loom, scattered nesting material (leaves, paper, string), and even droppings or urine stains.
The damage may not be immediately obvious —some rodents chew just enough insulation to cause an intermittent short or expose bare copper to a Grounded bracket.
Once you confirm rodent damage, the affected section of wiring will need to be repaired or replaced —just like any other physical harness damage.
Engine Wiring Harness Inspection Basics
The key to troubleshooting a short to power (in a sensor circuit) is a methodical inspection of the engine wiring harness. It's important to start off by looking for obvious physical damage:
- Inspect high-heat and rub zones: Look for damage near hot areas (exhaust, O2 sensors) or sharp edges that may have cut through insulation.
- Look for contact points on brackets, fuel rails, AC compressor mounts, or behind the engine near the transmission bellhousing.
- Check for melted sections: Inspect the engine wiring harness for melted insulation or broken loom.
- Test for voltage bleed at other sensors: Unplug sensors and test their wires individually for unexpected battery voltage.
- Examine fuse boxes for heat damage: Look for melted plastic, burnt terminals, or signs of overheating at fuse and connector slots.
- Inspect for signs of rodent damage: Chewed wires, shredded loom, nesting debris, or droppings near the intake, battery, or firewall.
How To Fix An Engine Wiring Harness Short To Power Problem
If you've discovered a short to power in your engine wiring harness, you might feel like the truck is done for —that it's time to junk it. But that's not true.
I've dealt with this issue plenty of times and I can tell you that with the right approach, you can fix this.
However, I've got to make one thing crystal clear:
- If the repair isn't done correctly, you're putting your entire vehicle at risk.
A short to power, left unresolved —or repaired poorly— can overheat, arc, and eventually set your wiring harness (or your whole truck) on fire. So whatever path you choose, the first priority is safety and long-term reliability.
Depending on the severity of the damage, here are the three main options —along with some hard-earned advice for choosing the right one:
OPTION 1: Repair The Wiring On The Vehicle (Only For Small, Minor Damage)
This option is ONLY appropriate when the damage is localized, small, and isolated—like one or two wires that have been pinched, chewed, or partially melted but haven't burned adjacent circuits.
When it's OK:
- Only a few inches of wire are affected.
- No other wires in the loom are damaged.
- The insulation on neighboring wires is intact.
- The harness wasn't exposed to flame or heavy arcing.
When it's a terrible idea: If any part of the harness was fully melted or burned through, stop right there. Trying to patch this on the vehicle will result in:
- Unreliable operation.
- Fire risk.
- Wasted time when it fails again.
Tips for on-vehicle repair:
- Carefully peel back the loom and inspect all surrounding wires.
- Replace the damaged wire using the same gauge, and solder it, never crimp.
- Use heat shrink tubing, then wrap the area in high-quality black electrical tape.
- Zip-tie the repaired section to prevent vibration-related fatigue.
OPTION 2: Remove The Harness And Repair On The Bench (Best For Contained Damage)
If the damage is a little more involved —but still limited to a defined section of the harness— removing it from the vehicle and repairing it on the bench is the safest, cleanest way to go.
You can inspect every wire up close, check for additional hidden damage, and make precision repairs without working around engine components.
When this is a great choice:
- The harness is intact overall, but one area has melted, chewed, or shorted wiring.
- You have good access to remove the harness cleanly.
- You want to be thorough and avoid future electrical gremlins.
Tips for off-vehicle repair:
- Do not try to replace a thick section of the harness —like one made up of 20, 30, or more wires— with a bundle of new wires.
- It might seem like a fix, but it's not a reliable long-term one.
- Splicing and soldering that many wires creates an unmanageable bulge in the harness, making it difficult to reinstall and route cleanly in the engine bay. Over time, that bulk leads to rubbing, stress on the wires, and ultimately connection issues, shorts, or complete circuit failure.
- If that many wires are damaged, the entire harness or sub-harness should be replaced.
- Use the same gauge wire (original scrap harnesses are a great source).
- Solder all connections —no butt connectors.
- Clean solder joints: no sharp points, no stray copper strands.
- Cover each repair with heat shrink tubing, then an outer wrap of black electrical tape.
This method takes time, but it's the right kind of time —what you put in here pays off in long-term reliability.
OPTION 3: Replace The Engine Wiring Harness (Best For Extensive Damage)
If the harness is severely damaged, burnt across multiple wires, or melted deep into the loom, replacement is the only safe choice.
But this is where most people get burned (no pun intended). Not all harnesses are interchangeable —even if someone online says they are.
What to watch out for:
- The replacement harness must match the original in year, engine size, transmission type, and ideally the month of manufacture.
- Wiring changes often happen mid-year —even within the same generation of Dodge Ram pickups— so getting a close-enough harness is not good enough.
Best practices:
- Your best bet is a local junkyard where you can check the vehicle (for year, engine size, and transmission size) and physically inspect and remove the harness yourself.
- Avoid buying harnesses online unless you know the exact donor vehicle specs.
- If a listing says “fits 1998–2003,” it's a red flag. That's rarely true without modification —and PCM connectors, sensor layouts, and fuse box wiring often vary.
Even if you're not ready to pull a harness yourself, talk to the salvage yard. Many let you verify the match by letting you see the vehicle before purchase and will remove it for you.
Final Thoughts: A short to power can seem like the end of the road. But if you're methodical, patient, and make repairs the right way, it's completely fixable.
Just remember:
- Prioritize safety —poor and sloppy repairs can lead to catastrophic fires.
- Know your limits. If the damage is too deep or you're unsure, seek help or consider full harness replacement.
- Take your time. One good repair is worth more than ten quick fixes.
You're not just keeping wires alive —you're keeping the whole truck alive.
More 5.2L, 5.9L V8 Dodge Ram Pickup Tutorials
I've written several more tutorials for the V8 Dodge Ram pickups that may be of interest to you that you can find in this index:
Here's a sample of the tutorials you'll find in the index:
- Troubleshooting A Blown Head Gasket (1989-2003 5.2L, 5.9L V8 Dodge Ram Pickup).
- How To Test The TPS (1992-1996 5.2L, 5.9L V8 Dodge Ram Pickup).
- How To Test The MAP Sensor (1992-1996 5.2L, 5.9L V8 Dodge Ram Pickup).
- How To Test The Intake Air Temp (IAT) Sensor (1992-1997 5.2L, 5.9L V8 Dodge Ram Pickup).
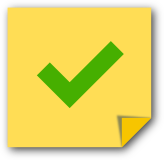
If this info saved the day, buy me a beer!
